What is manufacturing simulation?
Logistics is crucial to a company’s success due to rising production costs and globalization. Delivering on time and in sequence, introducing lean manufacturing principles, planning and building new sustainable production facilities, and managing global production networks require objective decision criteria to compare alternative approaches. Plant Simulation creates digital models of logistics systems so companies can optimize performance. The digital model allows users to run experiments and what-if scenarios without disturbing an existing production system. It can also be used in planning long before the real system is installed. Extensive analysis tools, statistics, and charts help users evaluate manufacturing scenarios and make fast, reliable decisions early in production planning.
Plant Simulation helps manufacturers to:
- Detect and eliminate problems that otherwise would require cost and time-consuming corrective measures during production ramp-up
- Minimize the investment cost of production lines without jeopardizing the required output
- Optimize the performance and energy usage of existing production systems by taking measures that have been verified in a simulation environment prior to implementation
Model in an object-oriented, 3D simulation environment
Create well-structured, 3D hierarchical models of production facilities, lines and operations for fast and efficient modeling of discrete and continuous manufacturing processes using powerful object-oriented architecture and modeling capabilities.
Build and visualize in 3D using included libraries or external CAD data. Leverage the JT data format for 3D modeling and Siemens direct model technology for efficient loading and realistic visualization of large 3D simulation models without compromising simulation and analysis needs.
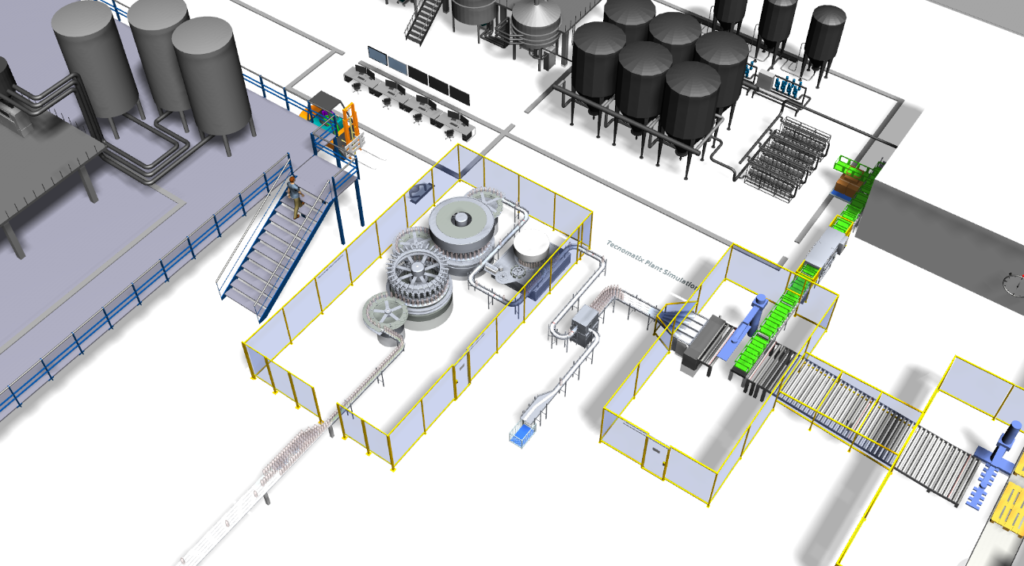
Benefit from inheritance and hierarchy
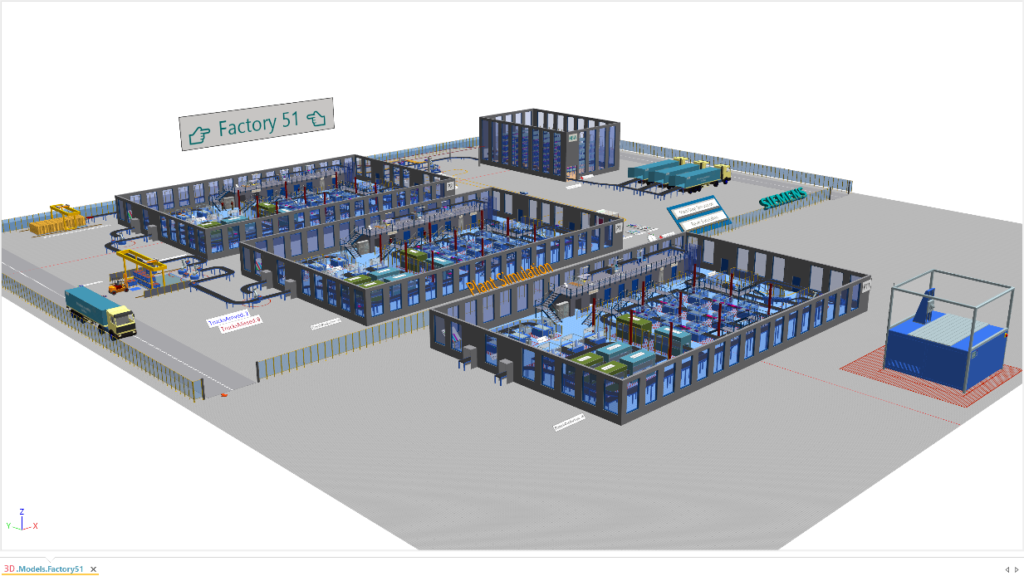
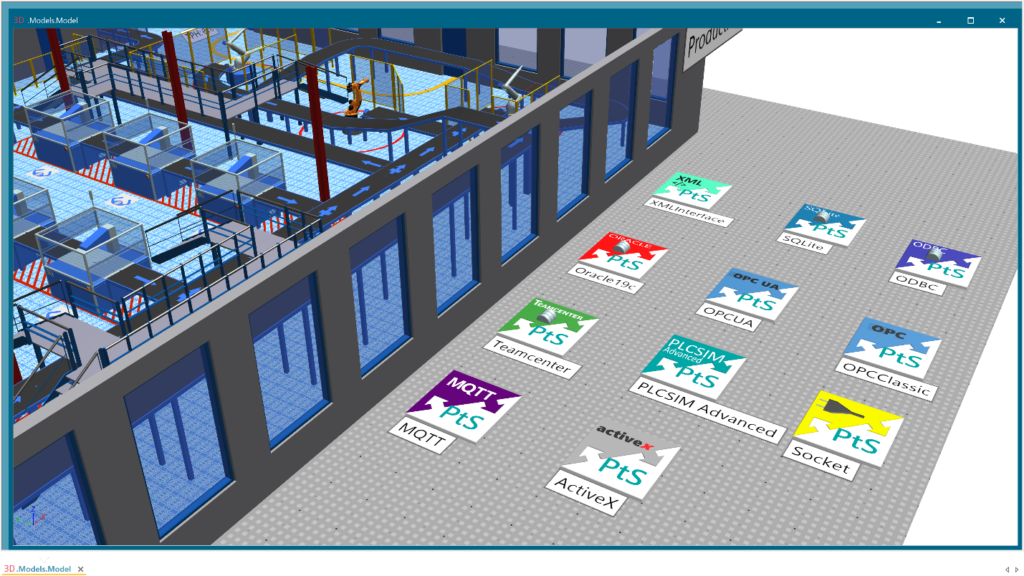
Handle, understand and maintain complex and detailed simulations much better than conventional simulation tools due to the architectural advantages of encapsulation, inheritance and hierarchy.
Model using objects within objects and models within models at all levels of the hierarchy. Items stored in libraries are maintained for all users and changes are automatically applied to all instances of those items wherever they are used. And those library items can be easily configured to specific requirements within a particular simulation
Take advantage of openness and integration
Leverage an open system architecture to support multiple interfaces and integration capacities, including ActiveX, C, CAD, COM, JSON, MQTT, ODBC, OPCClassic, OPCUA, Oracle SQL, Socket and XML.
Integrate easily with other Siemens software applications like NX Line Designer, Teamcenter, Simcenter HEEDS, Opcenter APS, TIA Portal, PLCSIM Advanced and SIMIT.
Analyze and experiment freely
including automatic bottleneck detection; throughput analysis; machine, resource and buffer utilization; energy consumption; cost analysis; Sankey diagrams and Gantt charts.
Use experiment management tools and integrated neural networks to enable comprehensive experiment handling and automated system optimization via genetic algorithms.
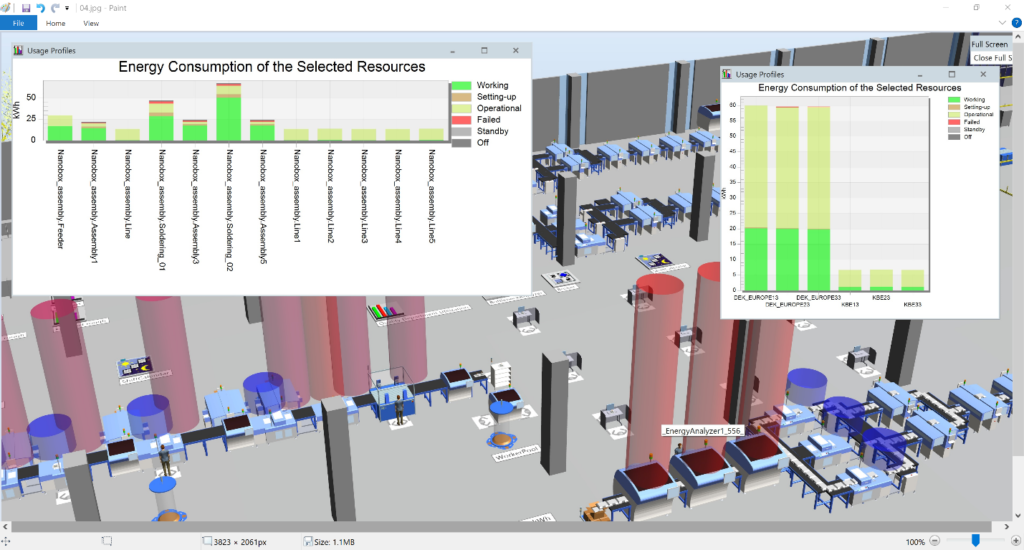
Example of Application :
Energy & Carbon Footprint
Business challenges
Manufacture energy-efficient car engines
Make components for differ-ent engine types on one line
Optimize production line for reduced energy usage
Maintain output, improve flexibility
Keys to success
Use Plant Simulation energy analysis functionality
Feed simulation model with measured values
Simulate production scenarios
Reprogram PLCs to introduce auto start-stop functionality in production machines
Results
Saved 3 million kilowatt hours of electricity per year with no hardware investment
Identified additional optimization potential
Reduced eco-footprint by 550 tons of CO2 equivalents per year
Scaled down lifecycle energy consumption of cars and SUVs
Using Tecnomatix, carmakers design and simulate complete production lines with machine tools and robot cells as well as material handling and transport systems. This gives them an opportunity to improve the production process by re-arranging factory floor layouts, thus accelerating production cycles and saving investment costs through optimized tool and machine utilization.
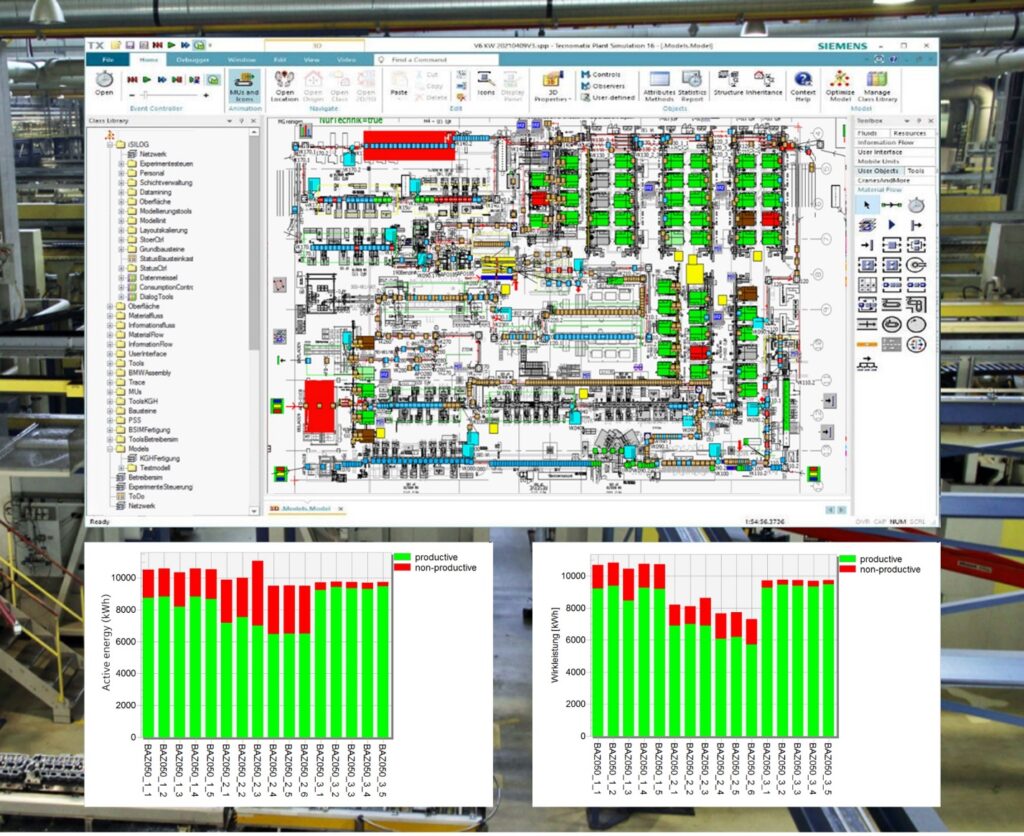
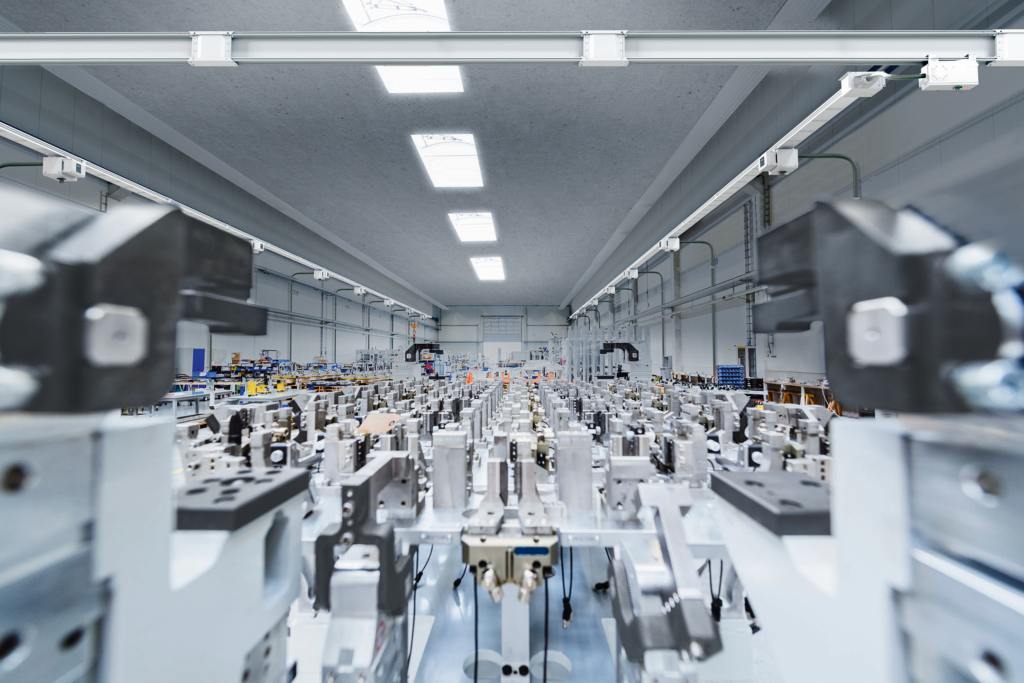
Plant Simulation is applied to solve production and logistic issues and optimize complex processes.
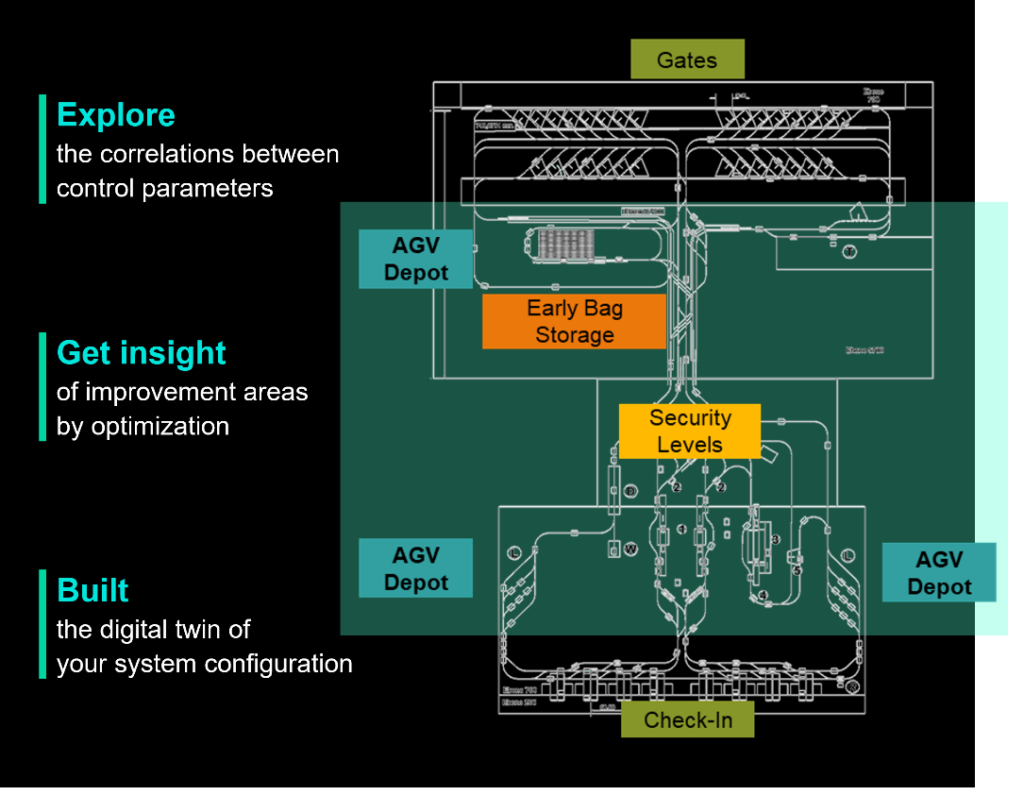
Logistics in Manufacturing by AGV
Highlights
- Number of required AGVs reduced by 13%
- Number of necessary charging stations
reduced by 17% - Overall costs reduced by 14%
- Identification of dependencies of battery
management - Efficient search for optimal system
configuration
The result Complex simulation processes for AGVs were optimized by closed loop
simulation based on artificial intelligence. With leading knowledge in simulation and validation of modern manufacturing technology, Siemens built the digital twin of an autonomous airport baggage handling system with AGVs to unleash optimization potential and provide the right
answers for future planning and actual decisions. Facts that speak for themselves: Number
of required AGVs and necessary charging stations were reduced. Overall costs were even reduced by 14%
Warehouse Simulation
Using a comprehensive digital twin to reduce high-bay warehouse commissioning time by 30 percent
Business challenges
Save storage space by devel-
oping a high-bay warehouse
Shorten the time for commis-
sioning a high-bay warehouse
Adopt virtual commissioning
to enhance efficiency
Keys to success
Use Plant Simulation to rapidly activate high-bay warehouse
Facilitate virtual commissioning to speed time to market Develop specific control programming with PLC and SCADA Leverage Siemens’ worldwide presence, excellent technology and strong partnership
Results
Reduced commissioning time
for high-bay warehouse by
30 percent Reduced the time necessary to achieve target availability by 88 percent
Improved the speed of delivering goods into the distribution cycle after production Detected about 95 percent of errors prior to the hot phase, significantly reducing stress
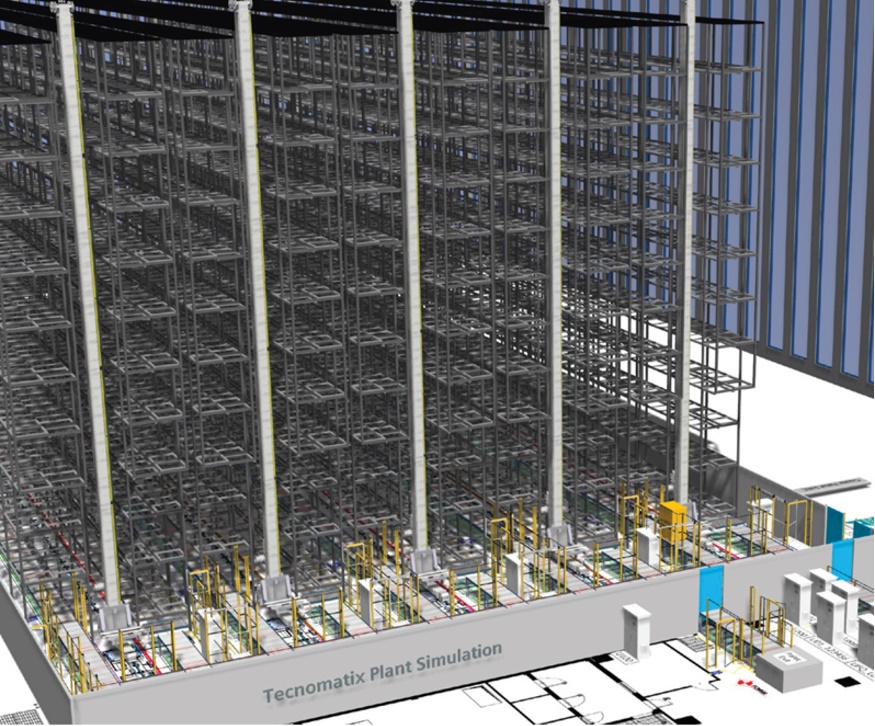
“The stability of the warehouse
has been visibly increased by the
virtual commissioning with
Plant Simulation.”