In recent years, the automotive industry has undergone a major transformation as internal combustion engine (ICE) vehicles gradually take a backseat, making way for electric vehicles (EVs). EVs have emerged as a sustainable alternative to reduce pollution and waste generated by fossil fuel combustion. As global demand for EVs grows rapidly, battery-powered electric motors are becoming the preferred clean and sustainable transportation solution.
However, the rise of EVs significantly impacts various aspects of vehicle design and manufacturing. One of the most critical factors to consider is the design of cable systems and wire harnesses within electric vehicles.
What is a High-Voltage Cable?
A high-voltage cable is specifically designed to handle high electrical voltages. Since EVs require significantly more power than conventional vehicles, they rely on large-capacity batteries to support long driving ranges. High-voltage cables are essential for efficient power transmission and ensuring the vehicle’s electrical system operates optimally.
Advantages of High-Voltage Cables in EVs
✔ High durability – Capable of withstanding high voltage, providing better power transmission, and offering superior strength compared to standard cables.
✔ Reduces the need for multiple smaller cables – High-voltage cables can carry larger amounts of electricity, minimizing system complexity and making wiring more efficient.
The Challenge: Strength vs. Flexibility
You probably heard about…Structure that prone to breakage without any signs!!
This principle applies to EV cable and wire harness design. The key is not just selecting the strongest materials but also ensuring the design meets practical application requirements.
Key Factors Affecting Cable and Wire Harness Design
1️⃣ Cable Material Selection
- The choice of materials directly impacts the flexibility, durability, and overall strength of the cables.
2️⃣ Design and Installation
- Improper installation can cause mechanical failures
- Cables and Wiring must be routed with sufficient space to accommodate movement. If cables are too tight or lack flexibility, they may experience stress accumulation, leading to material damage over time.
- Spatial constraints
- Limited space or obstacles within the vehicle can make routing more complex, increasing the likelihood of cable bending, twisting, or breakage.
3️⃣ Cable Size and Length
- The selection of appropriate cable size and length must align with the specific electrical load and installation standards. Cables that are too long or too short can affect performance and durability.
4️⃣ Mechanical Movements
- Different operating conditions cause cables and harnesses to move in various ways, including pulling, bending, and twisting. These movements create mechanical stress that can impact cable lifespan and reliability.
Unexpected Consequences: Problems from Poor Cable and Wire Harness Design
Poor cable and wire harness design or improper usage can lead to severe issues:
🚨 Rapid degradation and breakage – Using unsuitable materials or exceeding design specifications (e.g., excessive bending reducing bending radius) can cause early wear and tear.
🚨 Unnecessary material costs – Oversized or excessively long cables increase costs and may require additional space, leading to unnecessary expenses.
🚨 Delayed defect detection – Complex cable routing may result in unintended contact with other components, causing hidden damage that is difficult to detect.
🚨 Electrical short circuits and hazards – Improper design can accelerate component wear, increasing the risk of short circuits or even electrical fires, posing serious safety hazards.
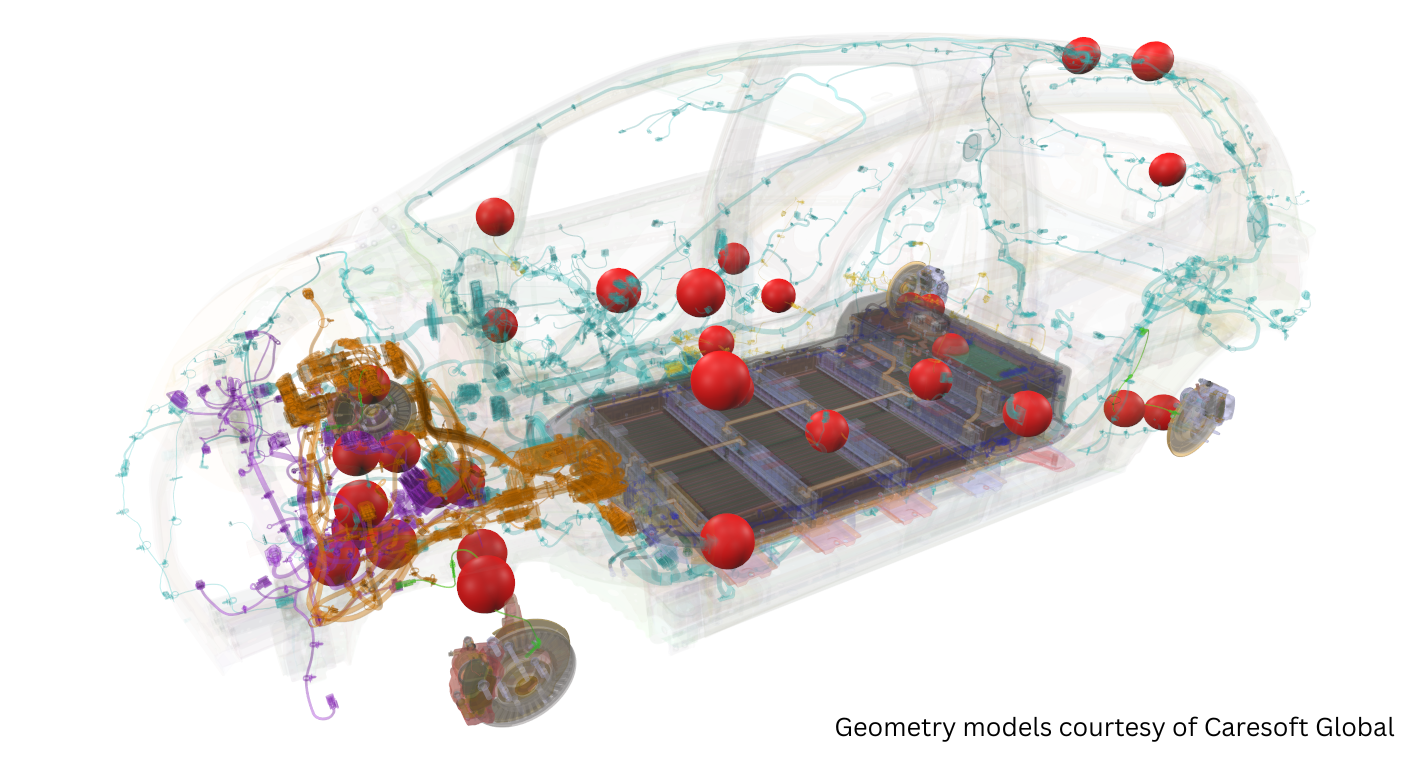
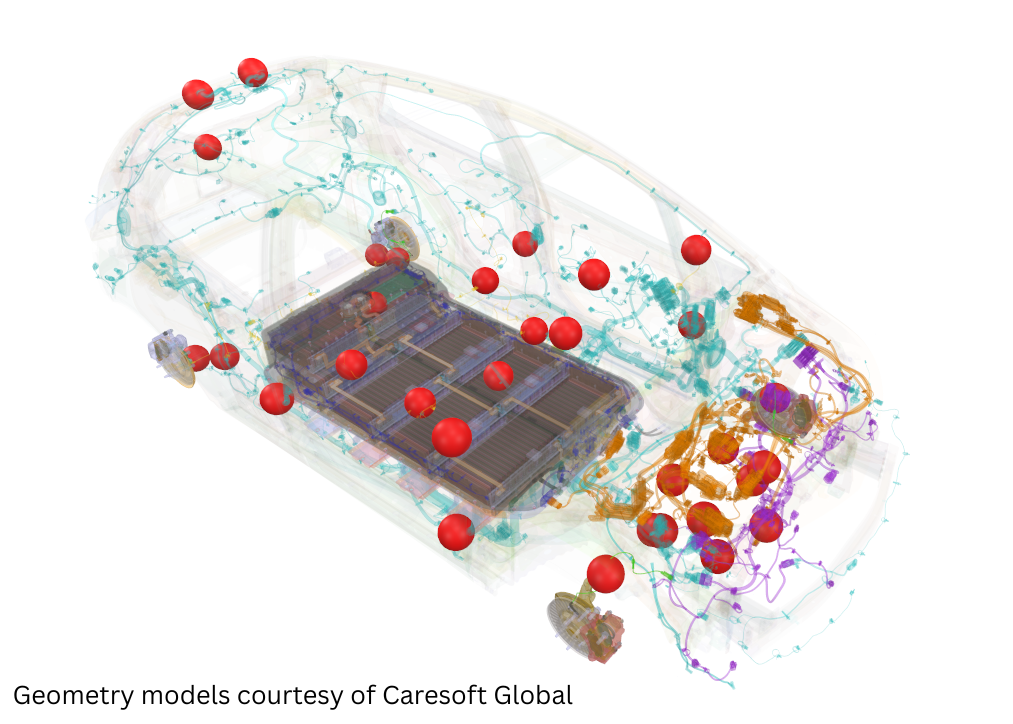
Conclusion
Cables and wire harnesses are vital components of an EV’s electrical system and must not be overlooked. Mechanical challenges arise when improper materials or inadequate design choices are made.
At Dentsu Soken Thailand, we offer IPS Cable Simulation – a CAE solution that enhances cable and wire harness design. Our solution allows engineers to accurately design wiring systems from the start, minimizing errors and improving production efficiency. 🚀
📅 Join our Webinar to enhance your Cable & Hose Design expertise!
🔗 Register here:
https://zoom.us/webinar/register/WN_nXC9QE0LSiSJKSqj2cRwPg#/registration
👨🏻💻 Written and Analyzed by:
Wuthipong Jintanasarn, CAD-CAE Application Engineer
A CAD/CAE solutions specialist with expertise in engineering design, simulation, and training. Experienced in motorcycle clutch testing, die-casting mold design, and coding for design optimization in the automotive industry. Holds a B.Eng. in Mechanical Engineering from Mahidol University. Former researcher in renewable energy, focusing on solar cells and wind turbines.
Connect Wuthipong‘s LinkedIn: https://th.linkedin.com/in/wuthipong-jintanasarn-4b32092ba