What is Lightweighting?
Lightweighting, or reducing the weight of components, is the process of minimizing product weight while maintaining optimal performance. Engineers achieve this by leveraging advanced materials and technologies to enhance efficiency, reduce costs, and improve environmental sustainability
Importance and Applications
Historically, lightweighting was primarily focused on the automotive and aerospace industries to reduce fuel consumption and increase travel range, such as in electric vehicles (EVs) and commercial airplanes. Today, other industries, such as electronics, medical devices, and transportation, are increasingly prioritizing lightweighting to meet the growing demand for sustainability and efficiency.
Approaches to Lightweighting
Lightweighting can be achieved through three main approaches:
- Material Substitution: Replacing traditional materials with lighter ones that offer equivalent or greater strength. The development of high-performance materials enables engineers to reduce weight without compromising critical properties.
- Design Optimization: Modifying component shapes or utilizing advanced technologies to reduce weight. For example, lattice structures can make parts lighter while maintaining their performance.
- Material Reduction: Advanced manufacturing techniques and materials allow for the removal of unnecessary parts without affecting safety or structural integrity.
This article focuses on the material substitution approach, specifically the shift from metals to plastics.
From Metal to Plastic: A New Era of Lightweighting
While metals are known for their strength and durability, they come with significant drawbacks:
❌ Heavy weight
❌ Susceptibility to corrosion
❌ High energy consumption during production
❌ Expensive production and maintenance costs
These limitations have driven the concept of “from metal to plastic,” emphasizing reduced weight and cost, increased corrosion resistance, and the consolidation of multiple metal parts into a single plastic component.
Fiber Reinforcement: Enhancing the Strength of Plastics
Adding fiber reinforcement to plastics, such as polypropylene, significantly enhances material strength and stiffness. For instance:
Properties of Polypropylene | Non-Fiber Reinforced | Fiber Reinforced |
---|---|---|
Tensile Strength | Lower | Higher |
Stiffness | Lower | Higher |
Ductility | Higher | Lower |
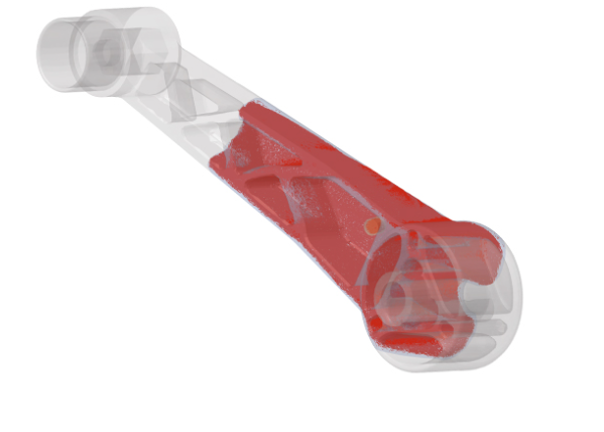
Key Insight: Fiber reinforcement results in anisotropic behavior, meaning the fibers increase strength and stiffness along specific directions. The arrangement of fibers, influenced by factors like mold shape, injection speed, and material flow, plays a critical role in determining the mechanical properties of the final product.
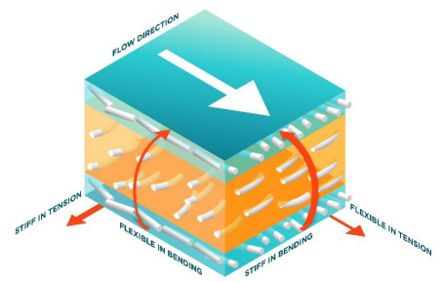
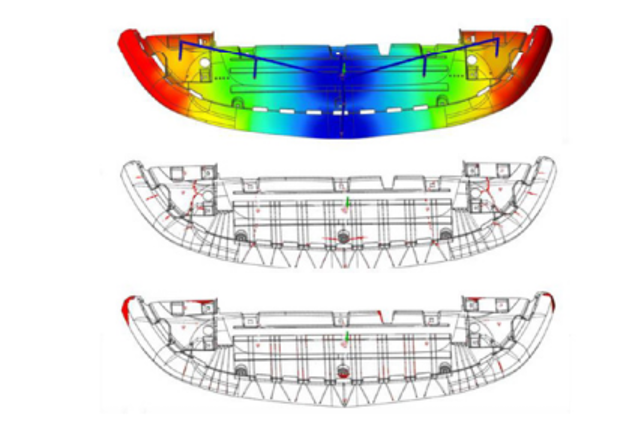
Understanding Fiber Orientation Through Injection Simulation
Studying the flow behavior during plastic injection molding is easily achieved through simulation.
Why is Injection Simulation Important?
Plastic injection molding is a complex process that directly impacts the quality of molded parts, such as viscosity changes due to shear rate or density variations with temperature and pressure. The process is transient, as plastics transition from liquid to solid states.
Advantages of Using Simulation
✅ Improved Decision-Making: Beyond structural performance, designers must consider manufacturability. Early-stage simulations ensure that the product can be manufactured, saving time and costs.
✅ Reduced Design Flaws: Simulations minimize defective parts, as fixing errors during production is costly.
✅ Faster Time-to-Market: Pre-production simulations streamline the design and development process, reducing iterations between design and production teams.

Altair Inspire: A Simulation Tool for Lightweighting
Altair Inspire enables users to perform real-time simulations of plastic injection molding. It provides an intuitive workflow to set up and analyze potential manufacturing issues, such as warping, shrinkage, or incomplete fills. This allows designers to test manufacturability and analyze results before molds are created, ensuring efficient production and high-quality outcomes.
Conclusion
Lightweighting represents a pivotal advancement in product design, addressing both sustainability and efficiency. The shift from metals to plastics, combined with fiber reinforcement, unlocks new potential for creating lightweight, durable, and cost-effective components across industries.
By leveraging tools like Altair Inspire for injection simulation, designers can better understand material behavior, reduce production errors, and accelerate time-to-market.
In an era where sustainability is paramount, lightweighting is more than just a design trend—it’s a critical strategy driving industries toward a more environmentally friendly and efficient future.
If you are interested in learning about Lightweighting Design,
Dentsu Soken Thailand is here to provide expert guidance. Contact us to learn more at:
📞 Tel: +66 (2) 632-9112
📧 Email: sales_th@th.dentsusoken.com
🌐 Website: www.th.dentsusoken.com
🟢 Line Official: https://bit.ly/DentsuSokenThailand-Line
🔵 Facebook: www.facebook.com/dentsu.soken.thailand
🔵 LinkedIn: www.linkedin.com/company/dentsu-soken-thailand-limited
🔴 YouTube: www.youtube.com/@Dentsu-Soken-Thailand
Supporting Documents for the Article
- Document: FROM METAL TO PLASTICS: SUSTAINABILITY, LIGHTER WEIGHT AT LOWER COSTS
- Learn more about the capabilities of Altair Inspire at: https://th.dentsusoken.com/th/products/altair-inspire-for-manufacturing/?swcfpc=1
👨🏻💻 Written and Analyzed by:
Nithikit Thanateerarangsan
Manufacturing Dept. Team Leader
CAE Solution Expert, With expertise in analyzing and designing aerodynamics for unmanned aerial vehicles (UAVs) using Computational Fluid Dynamics (CFD) techniques.