CAPABILITIES
Pre-Processing
Pre-processing involves preparing the model for analysis. This includes:
- Geometry Import & Cleanup: Import CAD models and repair geometry for simulation readiness.
- Meshing: Generate high-quality meshes tailored to the physics of the problem (structural, thermal, CFD).
- Material & Property Assignment: Define material behaviors, boundary conditions, and loading scenarios.
- Model Setup: Configure solver-specific parameters for accurate simulation
Post-Processing
Post-processing focuses on interpreting simulation results for actionable insights. This includes:
- Visualization: 2D/3D result plots, animations, and contour maps.
- Data Analysis: Extract stresses, deformations, temperature distributions, and performance metrics.
- Reporting: Create detailed reports and share results with stakeholders
Both tools enable engineers to validate designs efficiently and optimize product performance.
FEMAP
Benefits
Benefits of Using Pre/Post Processing Tools
- Improved Accuracy: High-quality meshing and precise boundary condition setup ensure reliable simulation results.
- Time Efficiency: Automation tools and user-friendly interfaces reduce model preparation and result evaluation time.
- Multi-Physics Integration: Seamlessly handle structural, thermal, and fluid interactions in a single environment.
- Flexibility with Multiple Solvers: Support for industry-standard solvers gives freedom to choose the best solution.
- Enhanced Visualization: Intuitive post-processing tools for quick interpretation and decision-making.
SIMCENTER 3D ENGINEERING DESKTOP
Modify any part quickly and easily –
even if you don’t know how it was originally created
- Intuitively edit geometry directly and on-the-fly
- Edit geometry independently of part feature history
- Bring imported, “dumb” geometry alive from multi-CAD sources
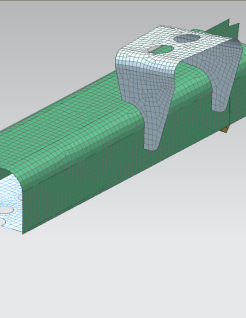
- Ideal for thin-walled parts
- Robust algorithms
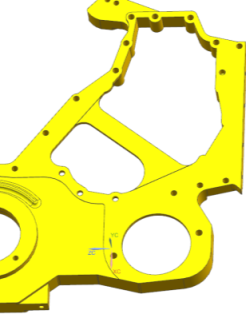
- Easily remove holes and blends
- Sew surfaces together
- Define mesh mating conditions

- Create geometry from mesh data
- Mesh becomes associative
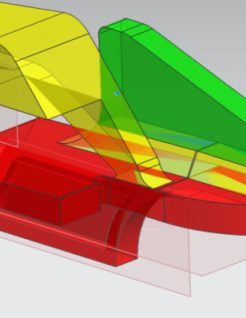
- Efficiently create sweep-able sections
- Creates associative solid bodies
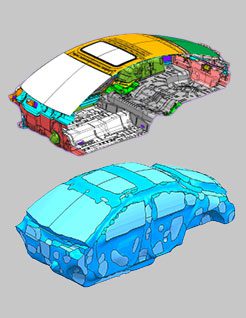
- Rapidly create fluid domain
- Associative to geometry updates
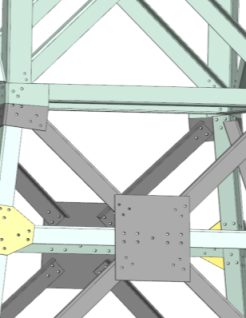
- Make complex edits
- Collaborate with design group
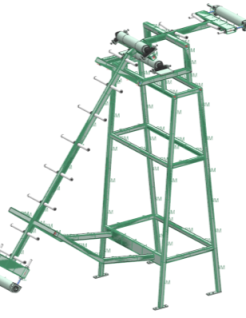
- Quick create and manage beam cross sections
- Connections, bolts and masses
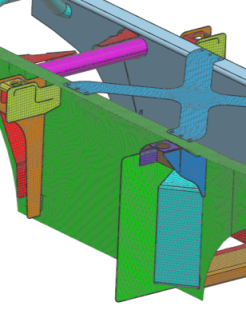
- Free or mapped meshes
- Analyzes surfaces to produce a better mesh
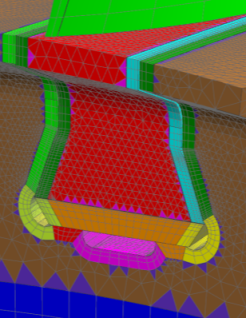
- Best-in-class tetra-mesher
- Use penta elements to transition from hex to tetras
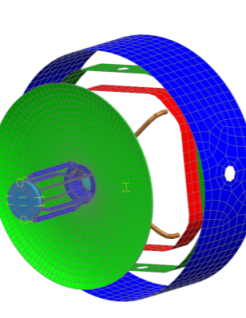
- Combine OD, 1D, 2D and 3D elements in a single model
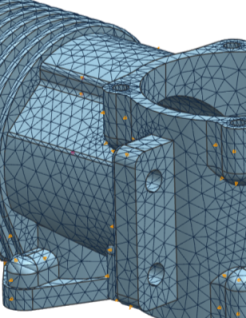
- Control mesh around holes, fillets and more
- Associative to geometry updates
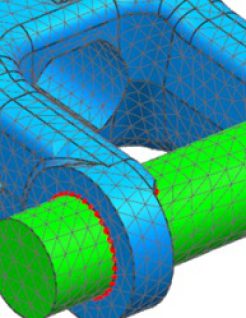
- Solver-based element checks
- Achieve more accurate solutions
SOLUTIONS
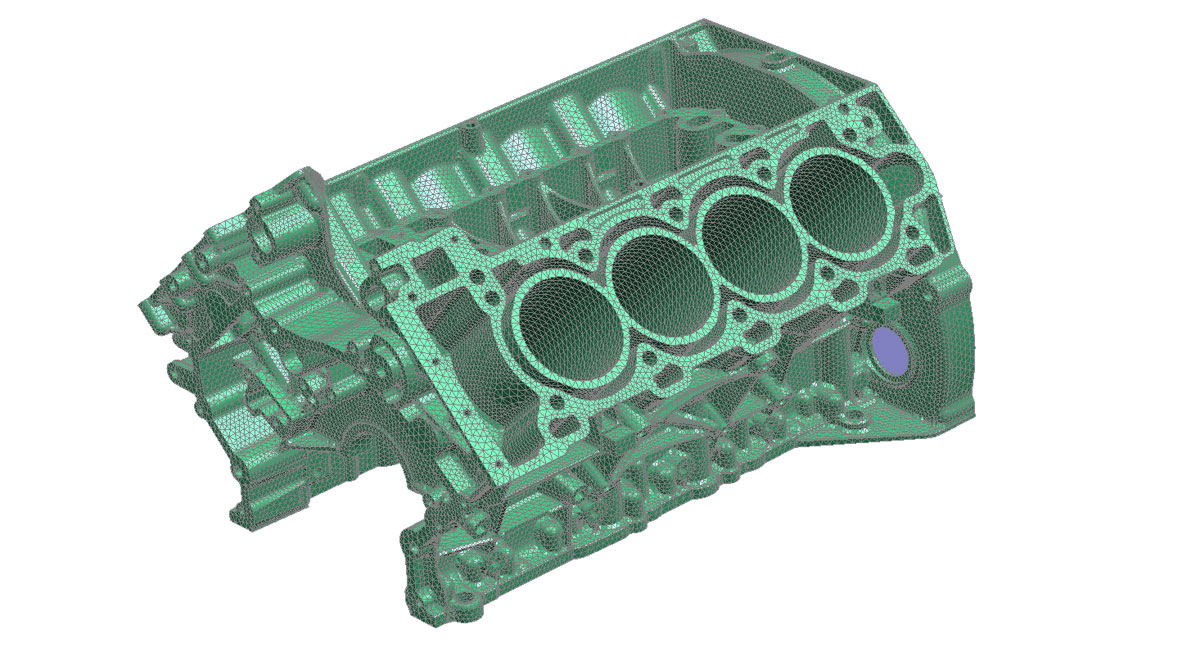
Simcenter 3D Desktop
A unified, open, and extensible CAE platform that empowers simulation analysts to perform advanced engineering analysis within asingle, integrated environment. It provides comprehensive tools for geometry handling, meshing, and multi-physics simulation setup, eliminating the need for multiple disconnected tools. Simcenter 3D integrates tightly with Simcenter Nastran and supports other leading solvers
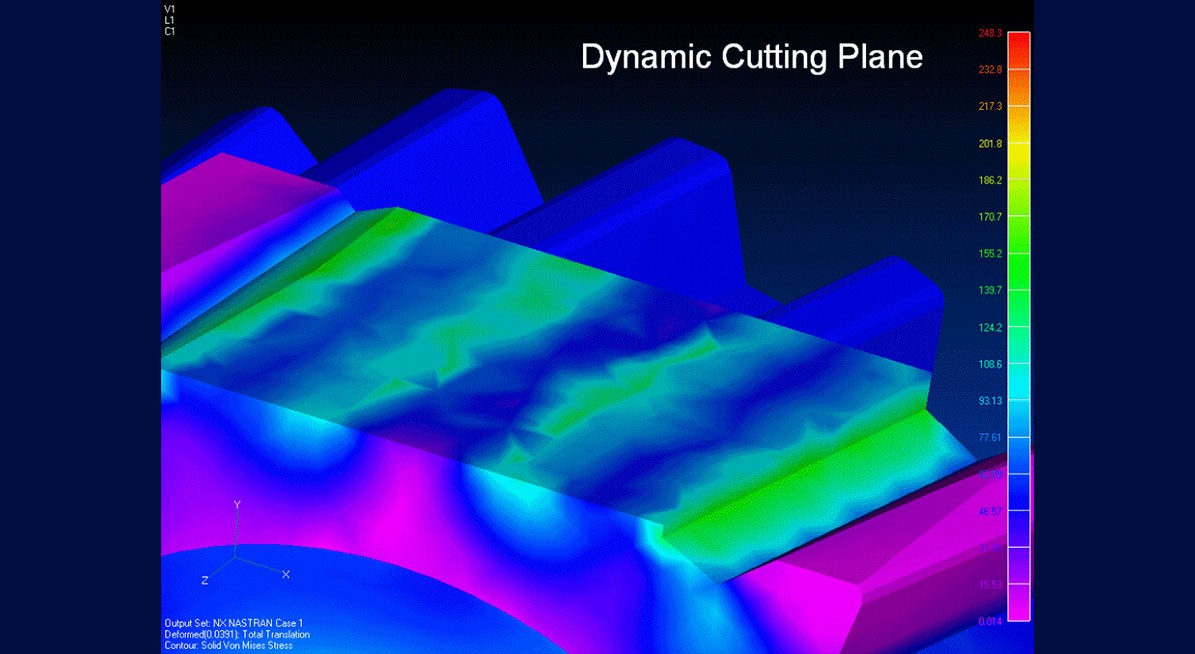
FEMAP
A leading finite element modeling (FEM) pre- and post-processing solution that combines power, precision, and affordability. Known for its ease of use and robust capabilities, FEMAP allows engineers to create detailed simulation models for a wide variety of engineering applications.
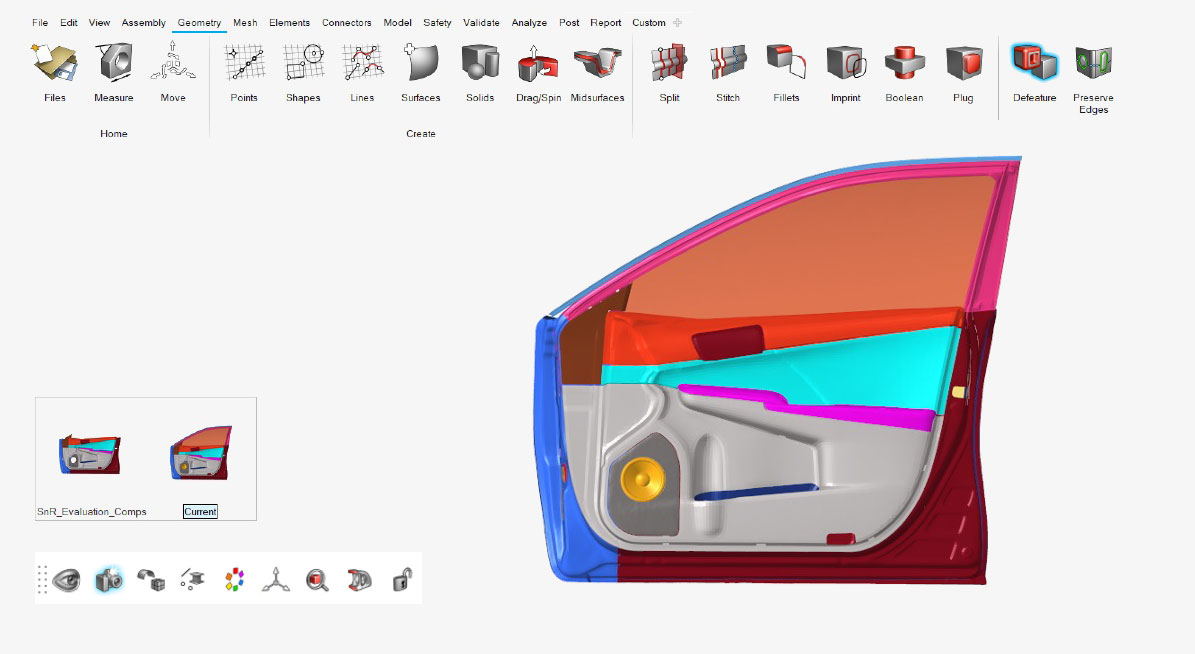
Altair HyperWorks
A comprehensive, open-platform CAE solution designed to streamline pre- and post-processing for advanced simulations. It provides robust tools for model interrogation, geometry handling, and high-quality meshing, ensuring accurate and efficient preparation for analysis across multiple physics domains